Technology Excellence Centers
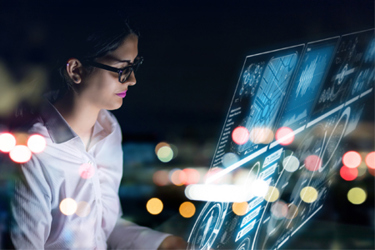
Comprehensive analytical and device testing services are available for injectable drugs, ensuring optimal primary packaging, compliance, and reliability throughout the product development lifecycle.
Selecting the right primary container for an injectable drug or passing a device design verification test are crucial steps in the product development process. So, the pressure is on to get it ‘right the first time. At Stevanato Group, Technology Excellence Centers (TEC) we can offer Analytical and Device Testing Services to support you all the way, from early-stage to launched combination product.
With our Areas of Expertise we can help you to find the right solution.
Custom Analytical Services
Stevanato Group is at your side throughout the drug development journey and can help devise customized tests and analytical services when required. Our scientific and technological expertise is available to help identify the root cause of complex issues. Leveraging our knowledge in primary packaging systems, we can then develop the right solution together.
Capabilities:
- Customized test methods
- Cooperation with R&D projects for testing (Method-Execution-Reporting)
- Fluid dynamics studies (Ansys)
- Tomography data elaboration
- Toxicological evaluation
- Regulatory Affair (i.e., Submission Support)
- Quality: QA and QC (Incoming and QC Release Test Method Development; Intercalibration-Comparability Studies)
- R&D (Test Method Development for New Products)
- Training (Norms, Regulation, Testing Procedures Etc.)
Container Interaction
One of the challenges facing the pharmaceutical industry is to ensure the best primary packaging system to guarantee the integrity, safety and efficacy of pharmaceuticals.
With their combined experience, Stevanato Group and Nelson Labs Europe are able to support customers in defining the most suitable primary packaging system through analyzing container-drug interactions.
Capabilities and testing
- Glass Tubing -Raw Simulation
- Glass Container Definition and Closures System Selection
- Simulation study
- Toxicological Evaluations on Extractable Data
- Full Toxicological Assessments on the Results of a Leachable Study
- Biocompatibility Testing (According to ISO 10993)
Container Performance
The physico-chemical properties of the materials have a strong impact on the performance of the entire container system. Container performance analysis embraces a diverse range of investigative fields, such as material, chemical, physical, mechanical engineering. Accurately testing the container performance (product/use-dependent) maximizes drug efficacy as well as device reliability and performance.
Our experts can assist you with selecting the right components, optimizing your device to improve performance with an existing container, compendial testing, as well as support in method development and validation of non-standard testing.
Capabilities and testing
- Visible and Sub-Visible Particles Counting and Characterization
- Break Loose-Gliding and Extrusion Force Testing
- Torque Force Testing (luer lock closures, caps etc.)
- Pull out Force Testing (Needles, Tip Caps, Needle Shields etc.)
- Compression Testing
- Breakage resistance testing (cone, flange, vertical and horizontal
- Burst test
- Tribology Testing
- Container Closure Integrity and Leakage testing
- Deliverable and dead volume
- Fractography and Failure Root Cause Investigation
- Coring and Fragmentation testing
- Stability and Stress Test
- Customized Functional Testing (Product-Dependent)
- Process mapping
Analytical techniques:
- Liquid Viewer
- Light Obscuration
- Micro Flow Imaging
- Dynamic Light Scattering
- Dynamometers: Gliding force/ Compression/Breakage resistance/Leakage testing/Torque force/Residual Seal force
- Optical Microscopes (Light, Stereo and DIC Microscopy): Surface and Material Imaging
- Nitrogen gas tracer AMI integrity test system
- Vacuum decay
- Dye Ingress methods
Surface Characterization
Many surfaces come in contact with the pharmaceutical product during its lifecycle. Our analytical experts can conduct a deep characterization of the physical-chemical properties of the surfaces, to correctly evaluate the container performance and the feedback when in contact with the drug product. The container surface investigation provides essential information to corroborate the physico-chemical performance of the system.
Capabilities and testing
- Surfaces Morphology Characterization and Imaging
- Defects Investigation
- Silicone Layer Characterization
- Contamination Identification
- Material Characterization
Analytical techniques:
- FE-SEM-EDX: High-Resolution Imaging and Elemental Analysis,
- RapID Layer Explorer/Bouncer: Silicone Layer Thickness and Distribution
- ZebraSci FLEX: Silicone Coverage
- FT-IR Spectrometer: Organic Compounds/Materials
- FT-IR Microscope: Organic Compounds/Materials at Trace Level
- Optical Microscopes (Light, Stereo and DIC Microscopy): Surface and Material Imaging
- Contact angle measurements: wettability of the surfaces and materials
Chemical Analysis
Partnering with Nelson Labs Europe, Stevanato Group’s laboratories can supply the most advanced and comprehensive chemical characterization of the primary packaging to detect and mitigate the risk of chemical interaction with drugs. We can assist in E&L analysis providing a multi-analytical approach for the selection of the proper container closure systems at each stage of the drug development journey.
Capabilities and testing
- Full Delamination Propensity Studies (According to USP <1660> Guideline)
- Extractables Studies on Polymer/ Rubber Container/Closure Components
- Pre-Screening and “Formal” Leachables Studies
- Identification of “Unknown Extractables” and Impurities in Drug Products
- Silicone quantification
- Tungsten Analysis
- Contamination Identification and Material Characterization
- Pharmacopoeias (USP, EP, JP) Testing
Analytical techniques:
- Headspace GC/MS: Volatile Organic Compounds
- GC/MS or GC/QQQ: Semi-Volatile Organic Compounds
- GC-Q-Tof: Semi-Volatile Organic Compounds
- LC/QQQ: Non-Volatile Organic Compounds
- LC/High-Resolution MS: Non-Volatile Organic Compounds
- UPLC-Q-Exactive Orbitrap: Non-Volatile Organic Compounds
- ICP/OES and ICP/MS: Metals & Elements (at trace level)
- Ion Chromatography: Anions
- FT-IR Spectrometer: Organic Compounds/Materials and silicone quantification
- FT-IR Microscope: Organic Compounds/Materials at Trace Level
- UV-Vis Spectophotometer: Transmittance Measurement
R&D fill and finish
De-risk commercial fill and finish earlier in the product development cycle.
Due to the long-lead time and high-cost of disrupting a commercial operation for an R&D or clinical activity, fill and finish machineability or compatibility testing is often performed after critical decisions like the finalization of the formulation and container closure.
Technology Excellence Centers offer small-scale replicas of industrial fill and finish setups, installed inside ISO-5 laminar air flow hoods in a laboratory environment, that can be used to prepare various containers (e.g., vials, syringes, cartridges) with various target media (e.g. viscous placebos, drug product).
This offering allows you to enhance your development and commercialization strategy while de-risking product and process:
- Demonstrate the machineability of your container, closure, and drug as early as the container selection phase.
- Improve the quality of your tests by using containers finished with representative vacuum or vent tube stoppering.
- Start process development before your commercial line even arrives.