Onsite Preclinical Services To Support Your Product Development: Powder Micromeritics
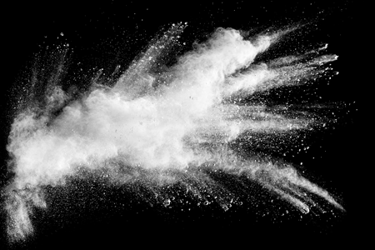
Understanding the fine details of powder properties is crucial in the pharmaceutical industry, where the behavior of particulate matter can affect manufacturability and the efficacy of the final product.
Natoli Scientific offers advanced on-site analysis of powder Micromeritics, which encompasses particle size distribution, flowability, and compaction properties. By assessing these critical parameters, our team helps in optimizing formulation and process development, ensuring that your product has a solid foundation for success from the onset.
Density Measurements
Accurate density measurements serve as a cornerstone for predicting powder behavior in various processing environments. Natoli Scientific employs state-of-the-art techniques to measure both tap and bulk density of powders—key indicators of the material’s ability to flow and compress. Understanding these parameters helps forecast how powders will interact with other substances, as well as their behavior during the tableting process. This data is crucial for quality control and ensuring consistent performance from batch to batch.
Bulk & Tapped Density Measurement
Our Bulk & Tapped Density Measurement services utilize precision instruments to measure the void space between particles, providing a clear picture of a powder’s ability to settle and thus its expected volume during packaging and storage. This understanding is pivotal when designing processes for material handling and storage, as it influences both equipment selection and quality assurance protocols. By offering in-depth analysis of these characteristics, Natoli Scientific ensures that potential challenges can be identified and addressed early in the product development lifecycle, paving the way for a smoother scale-up and commercialization process.
Helium Pycnometer
Natoli Scientific utilizes a helium pycnometer for precise density measurements, a technique esteemed for its accuracy and reliability. This instrument determines the true volume of a substance by measuring the volume of helium displaced by a powder sample. As helium atoms are small enough to penetrate the finest pores, the helium pycnometer can provide true density measurements that account for the closed porosity of particles. This level of precision is vital when designing pharmaceutical formulations, as it directly impacts the drug’s dissolution rate, bioavailability, and overall therapeutic efficacy. With a better understanding of material density, formulators can make informed decisions to optimize tablet weight and hardness, crucial factors in drug development and manufacturing.
Granule Characterization
Granule characterization is a pivotal phase in the pharmaceutical development process that Natoli Scientific rigorously addresses with its comprehensive on-site support services. By offering a deep dive into granule quality, our experts at Natoli Scientific uncover the critical attributes that can make or break a product’s performance — such as size, shape, and moisture content. High-quality granule characterization not only enhances the flow and compression of pharmaceutical formulations but also fortifies the integrity and dosage consistency of the finished product. Unlock the potential of your product’s development with Natoli’s precision-driven granule characterization and set the stage for a successful market entry. Discover the Natoli difference and how we can transform your granule challenges into a competitive advantage.
Particle Size & Distribution Measurement Using Sieve Analysis (d10, d50, d90)
Understanding the distribution of particle sizes within a batch is paramount in predicting the uniformity, dissolution, and bioavailability of the final pharmaceutical product. Our Particle Size & Distribution Measurement services leverage sieve analysis to pinpoint the dimensions of granules, with specific focus on the d10, d50, and d90 size fractions. These key metrics provide insight into the batch’s granulometric profile, indicating how 10%, 50%, and 90% of the sample’s population fall below a defined particle size, respectively.
This analysis is essential for ensuring content uniformity and is pivotal in the quality control stages of product development. By integrating this granular level of detail into our analysis, Natoli Scientific promises a thorough understanding of your product’s particulate attributes, contributing to the optimal efficacy and safety of the pharmaceutical preparation.
Moisture Analyzer (Loss on drying)
Natoli Scientific’s Moisture Analyzer testing, using the Loss on Drying (LOD) method, is a critical service for analyzing the moisture content of pharmaceutical granules. The LOD technique quantifies the amount of water or solvent released from a sample when subjected to controlled heating. Precise moisture analysis is essential since the presence of water can significantly impact the stability, flowability, and compressibility of the powdered material. Identifying and controlling the moisture level is fundamenttal in preventing negative effects on the physical and chemical properties of the final product, thus ensuring the integrity and efficacy of pharmaceuticals. Our skilled technicians utilize advanced Moisture Analyzers to provide accurate and reproducible data, contributing to the high-quality standards necessary for successful product development and regulatory compliance.
Powder Flow Measurements
At Natoli Scientific, understanding the flow properties of powder materials is seen as a fundamental aspect of preclinical development in pharmaceuticals. Our powder flow measurement services delve into the critical assessment of how powders move and behave under different conditions, an essential factor in ensuring a trouble-free manufacturing process. These examinations are instrumental in predicting potential processing difficulties and optimizing the flow properties that are crucial for consistent tablet production. Using advanced methodologies, Natoli’s expertise in measuring powder flowability equips clients with the data necessary to make informed decisions in the early stages of formulation development and equipment design.
FT4 Powder Rheometer
The FT4 Powder Rheometer is a versatile and sophisticated tool employed by Natoli Scientific for comprehensive powder flow measurements, especially during the critical preclinical stage of pharmaceutical development. This advanced rheometer is designed to simulate various processing conditions, thus providing a detailed characterization of powder flow properties under conditions that closely resemble those encountered during manufacturing. By assessing parameters such as flowability, compressibility, and shear properties, our scientists can predict how a powder will behave during processes like mixing, die filling, and compaction.
Insights gained from the FT4 Powder Rheometer enable us to optimize formulations before clinical trials commence, ensuring a robust and reliable manufacturing process, and paving the way for smoother regulatory approval and market success.
Angle of Repose
The “Angle of Repose” is a critical measurement conducted by Natoli Scientific to assess the flowability of powdered pharmaceutical materials. This fundamental test determines the steepest angle at which a pile of powder will stand, providing a direct indication of how a material will behave during handling, storage, and processing. By meticulously testing and recording the angle at which powder begins to collapse and flow under gravity, our team of experts can draw conclusions on the cohesiveness, density, and surface morphology of powder particles.
The result is an invaluable piece of data that is integral to predicting the behavior of the material during pharmaceutical manufacturing, such as the filling of capsules and die filling operations during tablet production. With a thorough examination of the Angle of Repose, Natoli Scientific aids clients in avoiding common manufacturing pitfalls, ensuring a more reliable and efficient production process.