Manufacturing Revolution In Life Sciences: Safeguarding Your Data As You Try To Get Ahead
By Petter Moree, Industry Principal, OSIsoft
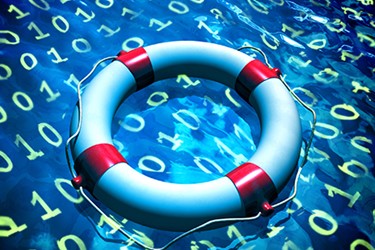
access the White Paper!
Log In
Get unlimited access to:
Trend and Thought Leadership Articles
Case Studies & White Papers
Extensive Product Database
Members-Only Premium Content
Welcome Back! Please Log In to Continue.
X
Enter your credentials below to log in. Not yet a member of ECM Connection? Subscribe today.
Subscribe to ECM Connection
X
Subscribe to ECM Connection