Dealing With Data Storage And Management In A Suboptimal Environment
By Grahame Morrison, Nexsan, A StorCentric Company
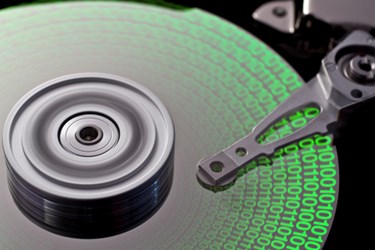
When you think about the mechanics involved in high-density storage systems, it becomes clear not every data storage system has the same level of reliability. We’re talking about incredibly small distances of less than the diameter of a human hair between the rotating disk and the heads that imprint data onto them. That doesn’t leave much room for error. And, when you consider that some storage solutions must operate in a less than ideal data center environment there are more factors to negotiate.
Consider these challenging environments that are less than ideal and beyond the norm due to vibration, temperature extremes, and remote locations with spotty service:
- Boats, research ships, and cruise ships
- Subway stations
- Small airport data closets
- Ground-based tracking (such as that used by NASA)
These are some of the reasons why the reliability of the storage system becomes so important. When a “data center,” per se, is not ideal and not well controlled, the key differentiator in product performance becomes a storage vendor’s design philosophy. This is even more critical than comparing disk vendors, since the reliability of data storage systems relies on additional factors along with disk drives. Attention to detail is a key component when it comes to reliability, starting with engineering and design, and incorporating storage system manufacturing and testing.
Some best practices that can help improve the operation and reliability of storage systems in less than ideal environments include the following:
An anti-vibration design. Without using anti-vibration design, storage system performance can suffer, particularly if the environment is not tightly controlled. By situating hard drives in pairs, stationed back-to-back, you can significantly decrease how much a vibrating drive affects the one next to it. Two other effective methods of vibration absorbance include mass and stiffness. By designing the chassis with thicker sections made from aluminum rather than steel, it’s rigidity instantly becomes superior. Fitting the drives with individual mounting rails also can help stabilize each drive.
Air flow for cooling. In addition to cutting down on vibration, strategically cooling the storage system can improve performance. The drives need a way to ensure that they stay cool consistently, which requires optimum front-to-back air flow via cooling fans. Multiple fans and blowers ensure redundancy to decrease the likelihood of a fan failing. Another benefit of the drives being arranged back to back is that it creates a channel for air to reach the drive’s electronics, which otherwise will quickly become hot. Drive temperature and fan speed will ideally be automatically and continuously monitored and adjusted for top performance. There are several advantages of using this strategy:
- Longer fan life
- Less noise
- Reduced consumption of power
Easy component replacement. Imagine being able to avoid downtime by replacing components even when the system is up and running. By using a feature where you can literally pull a drawer out while the system remains active, you improve consistency and reliability. This strategy also helps avoid loss of data access by providing more than one route for data to travel between host ports, disks, and RAID controllers.
Rigorous test procedures. Automated testing programs can identify weak drives, reducing the chance of failure and ensuring high reliability. Ideally, each drive produced for a storage system should undergo rigorous testing for quality control. An effective test cycle should validate, and subsequently repair as needed, each of the drive’s many sectors. If a predetermined number of sectors need correction, then the disk should be rejected, aiming for near perfection in order to qualify a disk. During testing, the best programs will monitor the disk performance problems.
Disk protection in transit. Damage can occur to disk drives during shipping and handling unless strict packing policies are followed to circumvent this possibility. This best practice is particularly important because when a disk is damaged in transit, it may not be noticed or flagged by the product’s internal self-tests. Careful preparation must therefore be applied before shipping occurs, as even minor bumps can stress the system, resulting in damage or failure in drives, mid-plane, and connectors. Ensure that all drives outside of the chassis are shipped in specially designed shipping containers to protect them in transit. A good benchmark for handling at the manufacturing stage is to specify that no drive be handled more than three times.
Enterprises must ensure that their data storage system offers not only innovative design, but stringent testing procedures and accommodations for manufacturing, shipping, and handling. This combination leads to quality control and reliability—even in the shakiest of environments.
About The Author
Grahame Morrison is E-Series & BEAST Product Director for Nexsan, A StorCentric Company joined Nexsan in 2014 as the Director of Product Development for the E-Series P and BEAST high density storage products. As the block storage Product Manager, he works closely with sales, marketing and, channel partners to ensure the roadmap of new features/functions meets end user needs. He also focuses on Nexsan’s next generation of product which will provide even greater performance and enterprise functionality whilst maintaining industry leading cost benefits.