Change Management Program For Cleaning And Disinfection
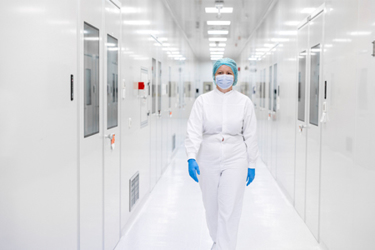
In such a highly regulated environment, change is not undertaken lightly. As a result, a lack of internal resources can often obstruct the implementation of change.
Continuous improvement fuels advancements in practices throughout the pharmaceutical industry, spearheaded by an FDA initiative. Numerous factors contribute to the ongoing enhancement of your cleaning, disinfection, and bio-decontamination protocols, including:
- Quality & Compliance
- Operational Efficiency
- Global Harmonization
- Sustainability
- Safety
- Cost Savings
- Global Technical Consultants
Our expert team of Global Technical Consultants can help make positive changes to your processes, driving continuous improvement that helps meet quality and regulatory requirements and business objectives.
With extensive industry experience in key areas including regulatory compliance, residue management and disinfectant efficacy validation, a partnership with Ecolab provides expert guidance and implementation support to ease the burden of change in your cleanroom.
Ecolab’s Change Management program provides you with a customized plan that meets your specific needs, supporting you through an end-to-end process, comprising one or more of the following elements:
Risk Assessment
Identifying the Need for Change:
- On-site/virtual assessment of contamination risks against industry regulations and best practice
- Detailed reporting of risks and mitigations supporting the contamination control strategy
Supplier Assurance
Assess Suitability of Your Supplier:
- Vendor qualification support
- Documentation to support your change control process
Product Selection
Selecting the Products and Equipment to Implement:
- Support with automated and manual product selection specific to your requirements
- Bespoke regime designed to mitigate contamination risks
Validation
Prove the Selected Agents and Regime Control Contamination Within the Facility:
- Validation project management
- Disinfectant efficacy testing
- In-situ validation study planning
Implementation
Generating the Resources Required for the Execution of Your Operation:
- Updating/creating standard operational documents
- Training theory and practice
- Ongoing technical support service